Pharmaceuticals: Leading solutions for mission-critical operations
AQUAANALYTIC offers a comprehensive approach to the implementation of cleanroom monitoring projects. We also supply components for equipping water treatment lines with electrodeionisation modules and UV reactors.
AQUAANALYTIC meets the needs of production laboratories with water treatment systems of the required water quality. Our systems are designed for a variety of applications, including the production of medicines, medical devices, cosmetics, personal care products, vision care, etc.
Pharmaceutical cleanrooms
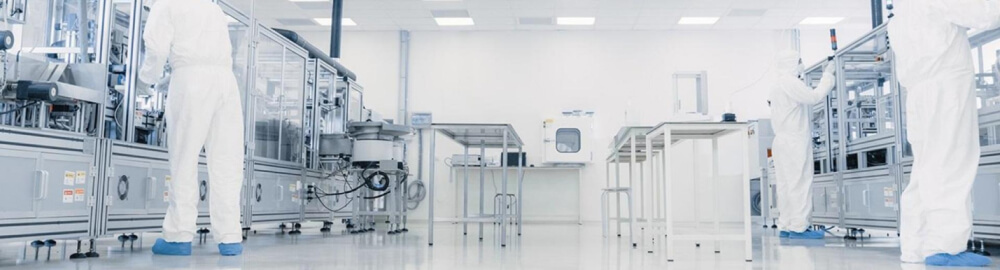
Pharmaceutical plants rely heavily on cleanrooms to ensure the sterility and safety of their products. Cleanrooms are controlled environments where contaminants such as dust, viable and non-viable aerosol particles and chemical vapours are kept to a minimum. Such facilities are essential for the production of medicines and vaccines, where even the slightest contamination can lead to product quality degradation and patient safety risks. Cleanroom design involves the use of high-efficiency HEPA filters to capture particles, maintaining positive air pressure to prevent contaminants from entering, and strict protocols for personnel entering the room, including the use of special clothing.
Monitoring of airborne particles
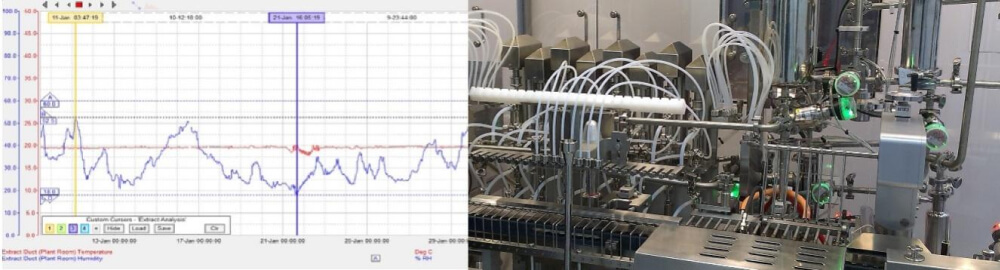
Particle monitoring in pharmaceutical plants is crucial for monitoring compliance in cleanrooms. This process involves continuously measuring the concentration of particles in the air to detect any deviations from acceptable levels. Particle counters and microbiological air samplers are widely used tools that provide data to help confirm compliance. Continuous particle monitoring systems help prevent contamination incidents and ensure that air quality meets the stringent regulatory standards set by agencies such as the FDA and EMA, thereby ensuring the safety of the manufacturing process.
Water treatment system components
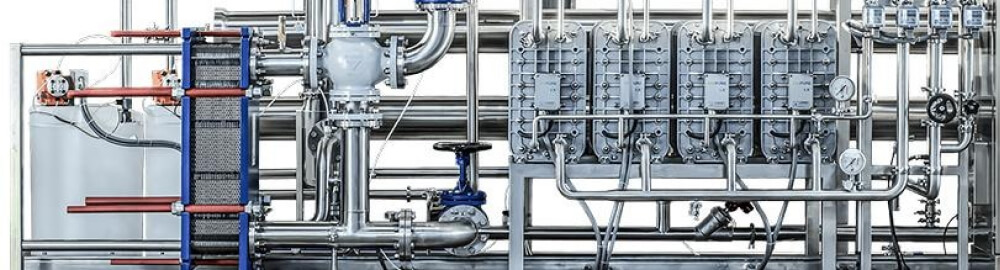
Purification of process water is another important component of pharmaceutical production. Water used in the production process must meet the highest standards of purity, as it can be a source of contamination. Purification systems typically include several steps, such as filtration, softening, reverse osmosis, deionization, and ultraviolet sterilization to remove impurities and microbial contaminants. Treated water must be continuously monitored to ensure compliance with pharmacopoeial standards, such as USP and EP. Proper water treatment is the foundation of the quality and safety of the manufactured pharmaceutical products.
Aerosol Disinfection
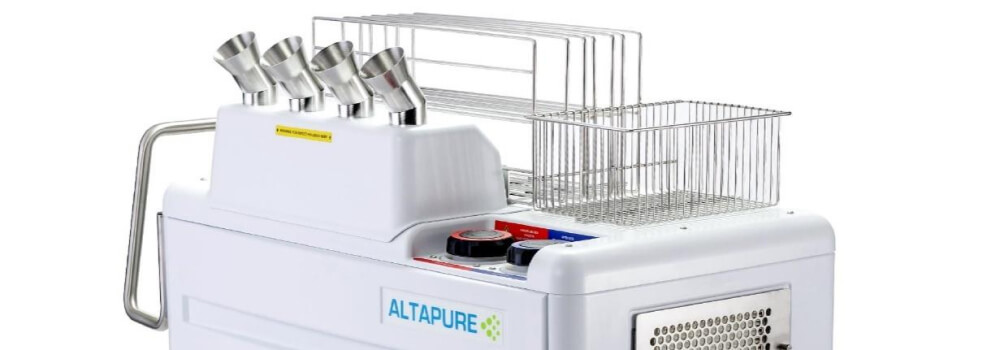
No-touch disinfection (NTD) systems typically use hydrogen peroxide vapor (VHP) or ultraviolet (UV) radiation in their operating principles. Both technologies have their advantages and disadvantages, but the undeniable advantage of non-contact disinfection systems is the minimization of dependence on operator errors. Altapure technology is able to create a large dense cloud of submicron-sized droplets — Sub-Micron Dense Fog (SMDF). The small size of the droplets of the special disinfectant allows the aerosol to quickly penetrate the treated area and interact with surfaces regardless of their geometry, location or distance from the Altapure device. Highly effective treatment of various surfaces (including any equipment or objects inside) is achieved by completely covering all exposed surfaces in the treated space.
Products
Request a quote
You can trust the 10-year experience of our engineers in striving to provide the best solutions for your business!